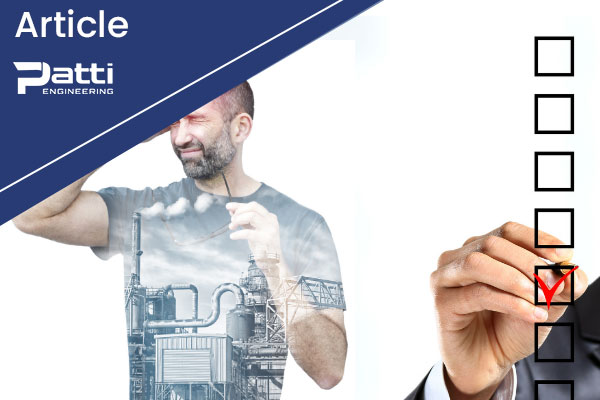
What is your plan when your equipment goes down?
Blog post by Dave Foster, Vice President of Engineering
It’s not a matter of if your equipment is going to go down, but when. The impact of this inevitability on your facility can vary drastically based on your team’s level of preparedness. Below is a checklist of aspects to consider to protect yourself from costly, lengthy, unexpected downtime.
Assess Your Risk
Do you know the impact downtime of given equipment will have on your overall process? Depending on how critical each piece of equipment is, you may want to consider:
- Maintenance: Are you doing effective preventative maintenance to avoid problems?
- Monitoring: Are you tracking/trending to identify events before they take you down?
- Inventory: Do you keep any inventory to maintain supply during down events?
- Employee utilization: Are workers idled during down events – how can you keep them utilized?
- Budgeting: Do you have long terms plans in place to upgrade/replace equipment BEFORE it becomes a support problem? Are you budgeting now?
Unexpected Downtime
Despite best-laid plans, there are occasional surprises. If your facility goes down unexpectedly, do you have a support structure that you can rely on?
If you have in-house expertise:
- How well do they know the process/technology?
- Do they work with the equipment and software daily? Or will they be getting back up to speed in the event of an emergency?
- Are they keeping up to date on the latest tools?
If you rely on outside contract support:
- Are they available to respond quickly?
- Is your point of contact up to date?
- Do you have a service contract to guarantee their availability?
- Do they still have the expertise to support your aging equipment?
Availability of replacement parts:
- Do you have spares in-house?
- Does your local supplier maintain inventory?
- Are the parts even still available, or are you searching eBay?
There is a LOT of life left in older equipment in facilities across the world, but you have to plan for the changing needs of the equipment as it ages. Just because a supplier carried a part three years ago doesn’t mean they still have it in stock today. Not unlike driving an older car or maintaining an older house, it can be a good financial decision to get the full lifespan of the equipment – as long as you are simultaneously planning for the end of the lifespan. Having answers to these questions will help you get a LONG ways toward getting all the life you can out of your equipment investments – without exposing yourself to unnecessary risk.
Related categories: Blog Company